Nickel-Chromium (Ni-Cr) metal foam is a type of porous material made from a nickel-chromium alloy. The production of Ni-Cr metal foam involves several key steps, each requiring specific techniques and equipment. Here’s an overview of the production process:
1. Raw Material Preparation
Materials: Nickel powder, chromium powder, and other possible alloying elements.
Mixing: The powders are thoroughly mixed to achieve a homogeneous blend.
2. Foam Formation
There are various methods to produce metal foam, including:
Powder Metallurgy Method
Blending with Foaming Agent: The Ni-Cr powder blend is mixed with a foaming agent (e.g., titanium hydride, which releases gas upon heating).
Compaction: The mixture is compacted into a green body using a press.
Sintering and Foaming: The green compact is heated in a furnace. The foaming agent decomposes, releasing gas and creating pores in the structure. Simultaneously, the metal powders sinter together to form a solid matrix.
Polymer Sponge Method
Polymer Template: A polymer sponge is used as a template for the foam structure.
Slurry Coating: The sponge is coated with a slurry containing Ni-Cr powders.
Drying: The coated sponge is dried to remove excess moisture.
Pyrolysis: The dried sponge is heated to burn off the polymer, leaving behind a metal skeleton.
Sintering: The metal skeleton is further heated to sinter the metal particles together, forming a rigid, porous structure.
3. Post-Processing
Heat Treatment: Additional heat treatments may be applied to improve the mechanical properties and remove any residual stresses.
Surface Treatment: Depending on the application, surface treatments such as plating or coating may be applied to enhance corrosion resistance or other surface properties.
Ni-Cr metal foams have a wide range of applications due to their unique properties, including high surface area, low density, and good mechanical strength. Some key application areas include:
1. Energy Storage and Conversion
Battery Electrodes: Used as current collectors in batteries due to their high surface area and good electrical conductivity.
Fuel Cells: Employed in fuel cell electrodes to provide a large surface area for electrochemical reactions.
2. Thermal Management
Heat Exchangers: Used in heat exchangers to enhance heat transfer due to their high surface area and good thermal conductivity.
Cooling Devices: Utilized in cooling systems for electronics and other high-heat-generating equipment.
3. Catalysis
Catalyst Supports: Serve as supports for catalysts in chemical reactions, providing a high surface area for better catalyst dispersion and reaction rates.
4. Filtration
Air and Liquid Filters: Used in filtration systems to remove particulates from air and liquids due to their porous structure.
Acoustic Damping: Applied in soundproofing and noise reduction applications.
5. Lightweight Structural Components
Structural Panels: Used in aerospace and automotive industries to reduce weight while maintaining strength.
Crash Absorption: Employed in impact absorption components due to their energy absorption capabilities.
Key Benefits of Ni-Cr Metal Foam
High Temperature Resistance: Can withstand high temperatures, making it suitable for high-temperature applications.
Corrosion Resistance: Ni-Cr alloys are resistant to corrosion, which extends the life of components in harsh environments.
Mechanical Strength: Provides good mechanical strength despite its porous nature.
Conclusion
The production of Ni-Cr metal foam involves sophisticated techniques such as powder metallurgy and the use of polymer templates, by sintering and post-processing. Its unique properties make it suitable for a wide range of applications, from energy storage and thermal management to catalysis and filtration.
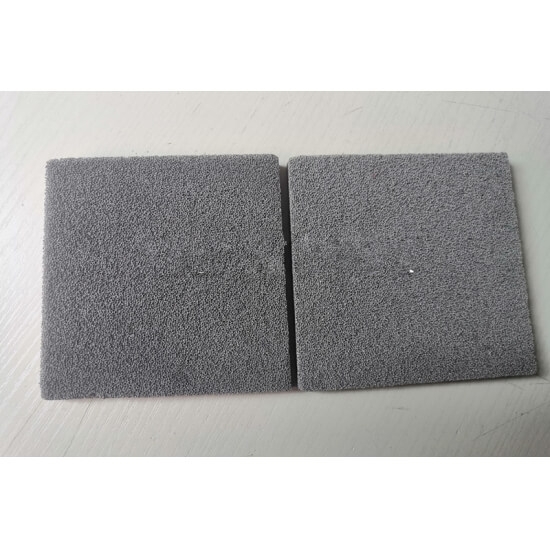