C Foam: Production Process, Applications, Advantages, and Challenges
Overview
C Foam, often referred to as Carbon Foam, is a lightweight, porous material composed primarily of carbon. It has unique properties such as high thermal and electrical conductivity, low density, and excellent chemical resistance, making it suitable for a variety of applications.
Production Process of Carbon Foam
Raw Materials
-
Precursor Materials: Commonly used precursors include coal, pitch, polymer resins, or graphite. These materials are chosen based on the desired properties of the final product.
Steps in Production
-
Precursor Preparation: The raw material is purified and prepared. This often involves mixing with binders or other additives to enhance the properties of the final foam.
-
Foaming: The precursor is heated to a temperature where it softens and forms a cellular structure. This can be done using:
-
Physical Blowing Agents: Gases like nitrogen or argon are used to create bubbles in the molten precursor.
-
Chemical Blowing Agents: Chemicals that release gases upon heating, creating a foamed structure.
-
Carbonization: The foamed precursor is subjected to high temperatures (600-1000°C) in an inert atmosphere (usually nitrogen) to convert it into carbon. This step removes non-carbon elements and solidifies the cellular structure.
-
Graphitization (Optional): For higher conductivity and enhanced properties, the carbon foam can be further heated to very high temperatures (2500-3000°C) in an inert atmosphere to convert it into graphite.
-
Post-Processing: This may include machining, surface treatment, or impregnation with resins or metals to improve specific properties.
Applications of Carbon Foam
-
Thermal Management: Due to its high thermal conductivity, carbon foam is used in heat exchangers, thermal interface materials, and heat sinks.
-
Energy Storage: Utilized in batteries and supercapacitors as electrodes due to its high surface area and conductivity.
-
Structural Components: Employed in aerospace, automotive, and construction industries for lightweight, high-strength components.
-
Environmental Applications: Used in filtration systems for water and air purification due to its porous structure.
-
Electromagnetic Interference (EMI) Shielding: Used in electronic devices to block EMI due to its conductive properties.
Advantages of Carbon Foam
-
High Thermal Conductivity: Efficient in thermal management applications.
-
Low Density: Provides strength and stiffness without adding significant weight.
-
High Surface Area: Beneficial for applications like energy storage and catalysis.
-
Chemical Resistance: Resistant to most chemicals, making it durable in harsh environments.
-
Electrical Conductivity: Useful in electrical and electronic applications for conductive pathways.
Challenges and Limitations
-
Cost of Production: High costs associated with raw materials and the production process, especially for high-performance carbon foams.
-
Brittleness: Carbon foam can be brittle, which may limit its use in applications requiring high impact resistance.
-
Scalability: Producing carbon foam at large scales with consistent quality can be challenging.
-
Material Uniformity: Achieving uniform pore size and distribution can be difficult, impacting performance in certain applications.
Development Challenges
-
Material Optimization: Continuous research is needed to improve the properties of carbon foam, such as enhancing mechanical strength and thermal stability.
-
Cost Reduction: Developing cost-effective production methods to make carbon foam more accessible for widespread use.
-
Environmental Concerns: Addressing the environmental impact of precursor materials and production processes, ensuring sustainable manufacturing practices.
-
Integration with Other Materials: Finding effective ways to integrate carbon foam with other materials without compromising its properties.
Conclusion
Carbon foam is a versatile material with a wide range of applications due to its unique properties. While there are significant advantages, challenges related to cost, production scalability, and material uniformity need to be addressed. Ongoing research and development are essential to overcome these hurdles and fully harness the potential of carbon foam in various industries.
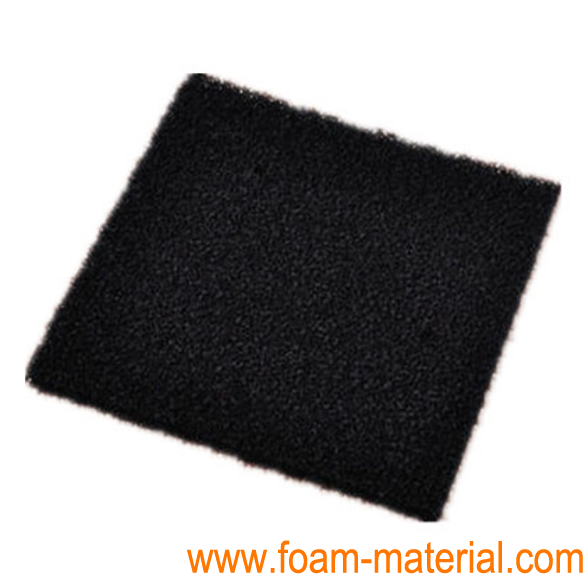