Zinc Metal Foam: Production, Applications, Advantages, and Challenges
Zinc metal foam is a porous material with a highly interconnected network of pores and a large surface area relative to its volume. This material combines the properties of zinc with the structural characteristics of a foam, making it suitable for various innovative applications. Here’s an in-depth look at the production process, applications, advantages, and challenges associated with zinc metal foam.
Production of Zinc foam
The production of zinc metal foam involves several steps, typically utilizing one of the following methods:
1. Powder Metallurgy Method
Mixing: Zinc powder is mixed with a foaming agent, usually titanium hydride (TiH2) or a similar compound.
Compaction: The mixture is compacted into a desired shape using a press.
Sintering: The compacted mixture is heated to a temperature where the foaming agent decomposes, releasing gas and creating a porous structure. The zinc particles sinter together, forming a solid yet porous metal foam.
2. Electrochemical Deposition
Preparation of Substrate: A conductive substrate is prepared, often a metal mesh or a foam template.
Electroplating: The substrate is immersed in an electrolyte solution containing zinc ions. An electric current is applied, causing zinc to deposit onto the substrate, forming a porous structure as the deposition process continues.
Template Removal: If a foam template is used, it is removed by chemical or thermal means, leaving behind a zinc metal foam.
3. Metal Melt Foaming
Melting: Zinc is melted in a furnace.
Foaming: A foaming agent is introduced into the molten zinc, creating gas bubbles that form a foam.
Solidification: The foam is cooled and solidified, retaining its porous structure.
Applications of Zinc Metal Foam
Battery Anodes: Zinc metal foam is used as an anode material in zinc-air and other types of batteries due to its high surface area and excellent conductivity, which enhance electrochemical performance.
Catalysts: The large surface area and porosity make zinc foam suitable for catalytic applications, particularly in chemical reactions requiring a metal catalyst.
Electromagnetic Shielding: Zinc metal foam can be used for electromagnetic interference (EMI) shielding due to its conductive properties and ability to absorb and dissipate electromagnetic waves.
Heat Sinks: The high surface area of zinc foam improves heat dissipation, making it an excellent material for heat sinks in electronic devices.
Filtration: Zinc foam's porous structure allows it to be used in filtration systems for gases and liquids, providing efficient contaminant removal.
Advantages of Zinc Metal Foam
High Surface Area: The porous structure provides a large surface area, beneficial for applications like catalysis and electrochemical reactions.
Lightweight: Zinc foam is much lighter than solid zinc, making it useful in applications where weight is a critical factor.
Good Electrical Conductivity: Retains the conductive properties of zinc, making it suitable for electrical and electronic applications.
Corrosion Resistance: Zinc has good resistance to corrosion, which extends the lifespan of products made from zinc foam.
Versatility: Can be used in a wide range of applications, from energy storage to filtration and EMI shielding.
Challenges in Using Zinc Metal Foam
Mechanical Strength: While lightweight, zinc foam may not have the mechanical strength required for certain structural applications.
Manufacturing Complexity: Producing zinc foam with uniform pore size and distribution can be challenging, requiring precise control over the manufacturing process.
Cost: The production of metal foams can be more expensive compared to traditional metal processing methods, which may limit their widespread adoption.
Material Properties: The properties of zinc foam can vary depending on the production method, which can affect performance in specific applications.
Environmental Impact: The production process, especially methods involving chemical agents, may have environmental implications that need to be addressed.
Development Challenges
Process Optimization: Improving manufacturing techniques to produce zinc foam with consistent properties and lower costs.
Material Innovations: Developing new alloy compositions and foaming agents to enhance the performance and applicability of zinc foam.
Scalability: Scaling up production processes to meet industrial demands without compromising quality.
Sustainability: Addressing environmental concerns related to the production and disposal of zinc foam, including recycling and waste management.
Conclusion
Zinc metal foam is a versatile material with unique properties that make it suitable for a variety of innovative applications. Its high surface area, lightweight nature, and good conductivity offer significant advantages, particularly in energy storage, catalysis, and thermal management. However, challenges related to mechanical strength, manufacturing complexity, and cost must be addressed to fully realize its potential. Ongoing research and development efforts are essential to optimize production processes, improve material properties, and ensure environmental sustainability, paving the way for broader adoption of zinc metal foam in diverse industries.
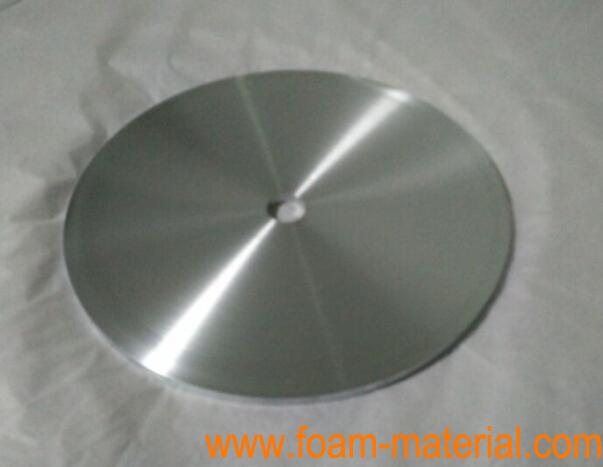