Exploring Nickel Foams: Versatile Materials for Modern Applications
Nickel foams are gaining significant attention across various industries due to their unique combination of properties. With applications ranging from energy storage to catalysis and thermal management, nickel foams are becoming essential materials in cutting-edge technologies. In this blog post, we will delve into what nickel foams are, how they are produced, their key properties, and the diverse applications that make them indispensable in today's technological landscape.
What Are Nickel Foams?
Nickel foams are porous materials made from nickel, characterized by their high surface area, low density, and excellent conductivity. Structurally, Foam Nickel consist of a network of interconnected nickel struts that form a three-dimensional framework with numerous open pores. These foams can vary in pore size, density, and thickness, allowing them to be tailored for specific applications.
The porous structure of nickel foams is what gives them their distinctive properties, making them particularly useful in applications where high surface area and conductivity are required.
How Are Nickel Foams Produced?
The production of Nickel Foam Sheet typically involves a few key processes, each designed to create the desired porous structure and material properties:
1.Electroplating on Polymer Foams: One common method involves using a polymer foam template. This foam is coated with a thin layer of nickel through an electroplating process. After the nickel layer is deposited, the polymer template is removed, usually through thermal decomposition, leaving behind a pure nickel foam.
2.Powder Metallurgy: In this method, nickel powder is mixed with a binder and a foaming agent. The mixture is then compressed and heated, causing the foaming agent to release gas and create pores within the nickel matrix. The binder is then removed, leaving a porous nickel structure.
3.Chemical Vapor Deposition (CVD): This technique involves the deposition of nickel from a gaseous phase onto a substrate, which can then be removed or retained depending on the desired final product. CVD allows for precise control over the thickness and pore structure of the nickel foam.
4.Direct Foaming: Nickel can also be foamed directly by injecting gas into molten nickel or by using foaming agents that generate gas bubbles in the metal during solidification.
Each of these methods offers different advantages in terms of pore size, structural integrity, and production cost, allowing manufacturers to choose the best approach for their specific needs.
Key Properties of Nickel Foams
Nickel foams possess several properties that make them highly valuable in various applications:
1.High Surface Area: The porous structure of nickel foams provides a very large surface area relative to their volume, which is critical in applications like catalysis and energy storage, where reactions occur at the material's surface.
2.Electrical Conductivity: Nickel is an excellent conductor of electricity, and the open structure of the foam allows for efficient current distribution, making it ideal for use in battery electrodes and other electronic components.
3.Mechanical Strength: Despite their low density, nickel foams maintain good mechanical strength and can withstand significant stress without collapsing, which is important for structural and load-bearing applications.
4.Corrosion Resistance: Nickel's natural corrosion resistance is retained in its foam form, making it suitable for use in harsh environments, including in chemical processing and marine applications.
5.Thermal Conductivity: Nickel foams also exhibit high thermal conductivity, which, combined with their porous structure, makes them effective for heat dissipation and thermal management in electronic devices and systems.
Applications of Nickel Foams
The unique properties of nickel foams have led to their use in a wide range of applications:
1.Energy Storage: One of the most prominent applications of nickel foams is in energy storage, particularly in nickel-metal hydride (NiMH) batteries and emerging battery technologies. Nickel foams serve as the conductive substrate for battery electrodes, providing a large surface area for electrochemical reactions and contributing to the battery's overall efficiency and capacity.
2.Catalysis: The high surface area and excellent conductivity of nickel foams make them ideal as catalyst supports in chemical reactions, including hydrogenation and reforming processes. The porous structure allows for better interaction between the catalyst and the reactants, leading to higher reaction rates and improved efficiency.
3.Thermal Management: In electronic devices, managing heat is crucial for maintaining performance and preventing damage. Nickel foams are used in heat exchangers, cooling pads, and other thermal management systems to dissipate heat effectively due to their high thermal conductivity and large surface area.
4.Filtration: The open, porous structure of nickel foams makes them suitable for use in filtration systems, particularly for gas and liquid filtration in chemical processing and environmental protection applications. The foam can trap contaminants while allowing fluids to pass through, making it an effective and durable filter medium.
5.Sound Absorption: Nickel foams can also be used in acoustic applications due to their ability to absorb sound waves. This makes them useful in noise reduction systems, particularly in industrial environments where noise control is important.
6.Electrochemical Devices: Beyond batteries, nickel foams are used in fuel cells and supercapacitors, where their high conductivity and surface area enhance the performance of these devices. In fuel cells, for example, nickel foam serves as an electrode material, facilitating efficient electrochemical reactions.
Future Prospects of Nickel Foams
As industries continue to innovate, the demand for advanced materials like nickel foams is expected to grow. Research is ongoing to improve the properties of nickel foams, such as increasing their mechanical strength, optimizing their pore structure, and developing new production methods that are more cost-effective and environmentally friendly.
The rise of renewable energy technologies, electric vehicles, and more efficient electronic devices will likely drive further advancements in nickel foam applications. Additionally, as the need for sustainable and efficient materials becomes more pressing, nickel foams are poised to play a crucial role in the development of greener technologies.
Conclusion
Nickel foams are versatile materials that offer a unique combination of properties, making them indispensable in a wide range of applications. From energy storage and catalysis to thermal management and filtration, nickel foams provide solutions to some of the most challenging problems in modern technology. As research and development in this field continue to advance, we can expect to see even more innovative uses for nickel foams, cementing their role as a critical material in the future of technology.
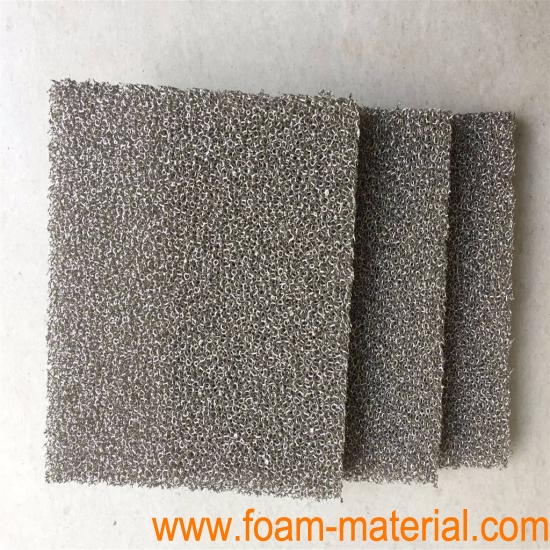